- Compressor selection problem
- Compressor search
- Do-it-yourself compressor removal from the refrigerator
- Features of refrigerators and their compressors
- Health Check
- Compressor station design
- Ways to purchase equipment
- Receiver problem
- Preparation and connection of the compressor from the refrigerator for use in the compressor installation
- Installing the air filter on the air intake
- Mounting the oil cleaner
- Highway with measuring and control equipment
- The problem of connecting instrumentation
- The problem of high pressure rubber tubes
- Do-it-yourself compressor maintenance
With the help of improvised tools and a standard set of household tools, any homeowner can assemble a home-made air compressor from the refrigerator. The scope of such an apparatus is quite wide and justifies the expenditure of forces and means for its manufacture:
- Air compressor for airbrushing and painting.
- Electric pump for inflating car tires.
- An energy source for a pneumatic tool.
- Air pump for purging complex mechanisms during their repair.
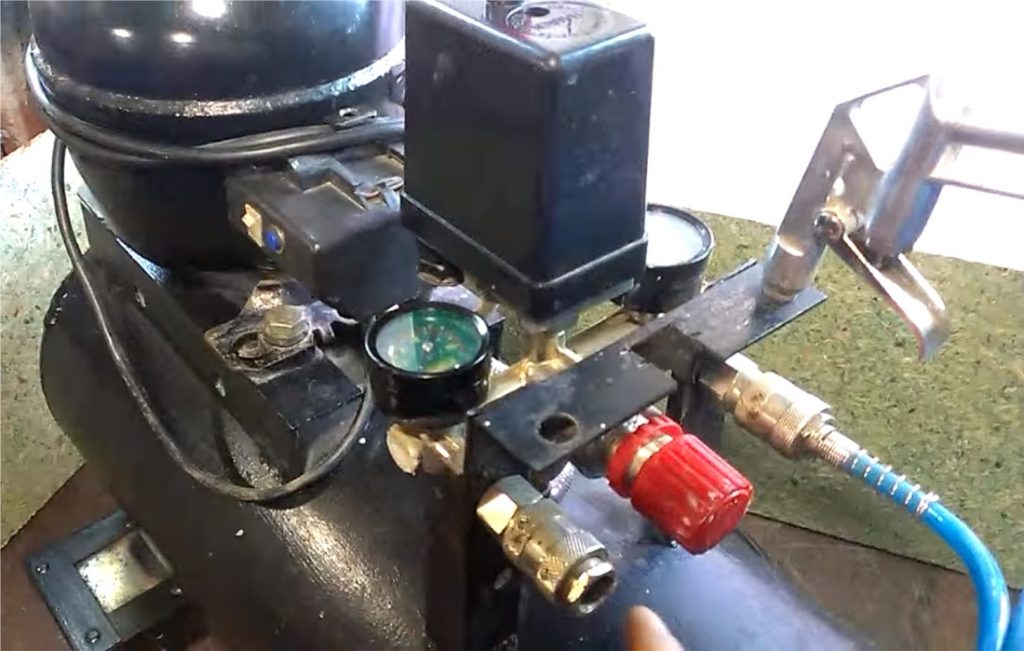
Homemade air compressor from the refrigerator
The range of capabilities, power, durability and reliability of a home-made system for generating compressed air, assembled on the basis of a compressor from an old refrigerator, depends on the correct design and installation of its elements.
Compressor selection problem
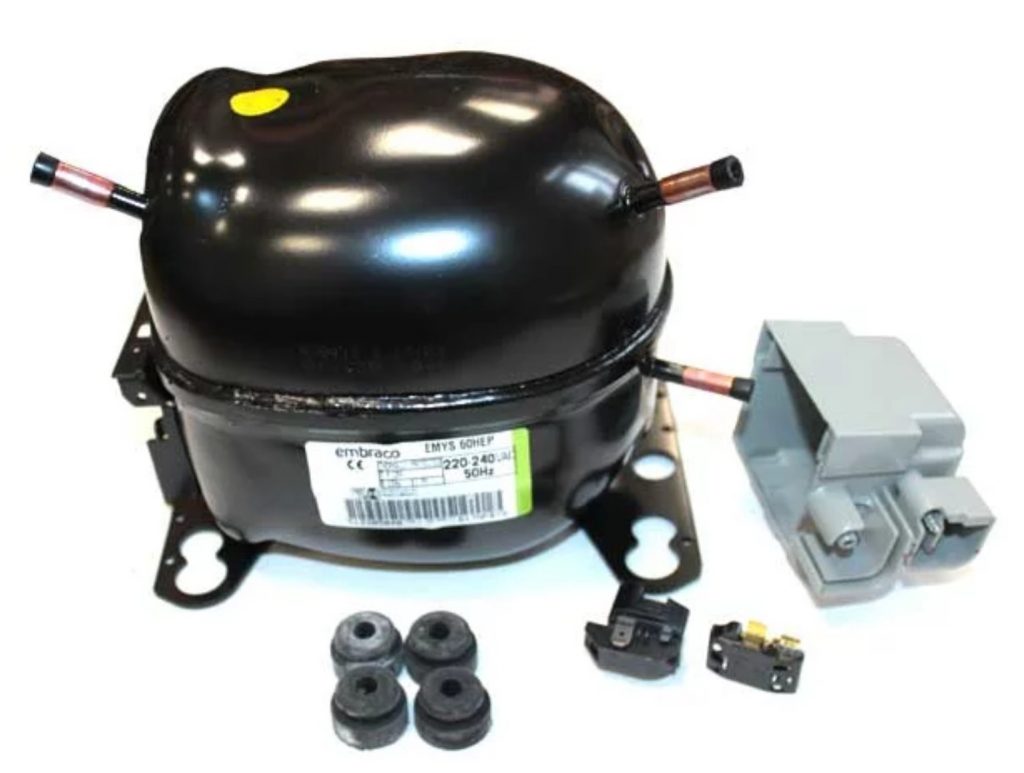
Compressor from an old refrigerator
The assembly of a functional and reliable apparatus begins with the selection of its main component - the compressor. It is available in any household refrigerator, acts as a pump for pumping refrigerant and is a single unit in a sealed metal shell, from the outside of which a relay is mounted to start it. To solve the problem, any similar motor in good condition is suitable. Further selection and configuration of all additional structural elements is determined by the shape and characteristics of a particular device.
Compressor search
If there is no old and unnecessary refrigerator at hand, then there is always the opportunity to purchase a dismantled unit in the market for used tools and spare parts. There you can buy a workable option for 100-150 rubles.
Do-it-yourself compressor removal from the refrigerator
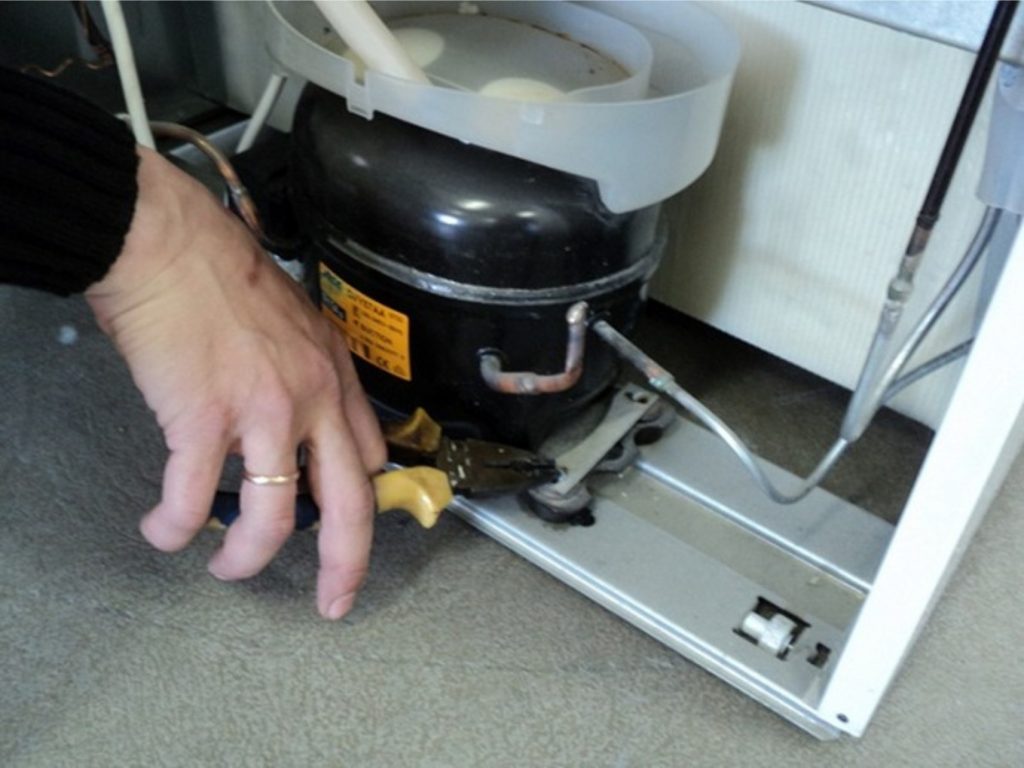
Do-it-yourself compressor removal from the refrigerator
Removing the device from the refrigerator can be done with ordinary wrenches and screwdrivers. It is better to bite the air inlet and outlet tubes, and not to saw off, so as not to clog the mechanics of the apparatus. A standard start relay is also dismantled.
Features of refrigerators and their compressors
The capabilities and characteristics of the compressor selected as the basis for the future compressed air supply should be considered. The options are as follows:
- The simplest solution is linear motors.
- Inverter motors.
Both options are suitable for work, but their features should be taken into account. Linear devices are designed for a constant speed. Therefore, they are better suited to create a compressor apparatus. Converter options are designed for variable speed, which should decrease depending on the signal from the temperature sensor.
Health Check
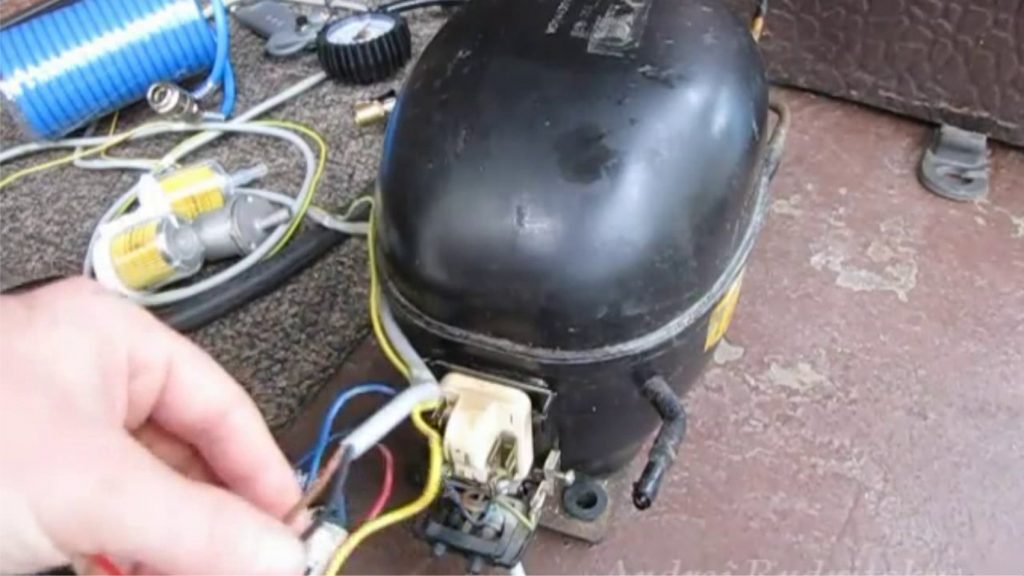
Checking compressor operation from the refrigerator
In order to check the operability of the unit, you should first ring it using an electronic resistance meter, and then connect it to the network:
- Each input contact is checked. Usually there are 3 units on the unit, configured for a standard relay connector.
- The contact with the maximum resistance refers to the starting mechanism of the electric motor (approximately 20-40 Ohms)
- Contact with a resistance of 10-15 Ohms refers to a winding that provides an operating mode (the wire on its winding is thicker).
- The third contact is phase.
For a test connection, the voltage is supplied to the working and phase contact, after which a short-circuit of the working and starting contact is made. The device should create a stable timbre of sound when turned on, and air should flow from the output tube.
Compressor station design
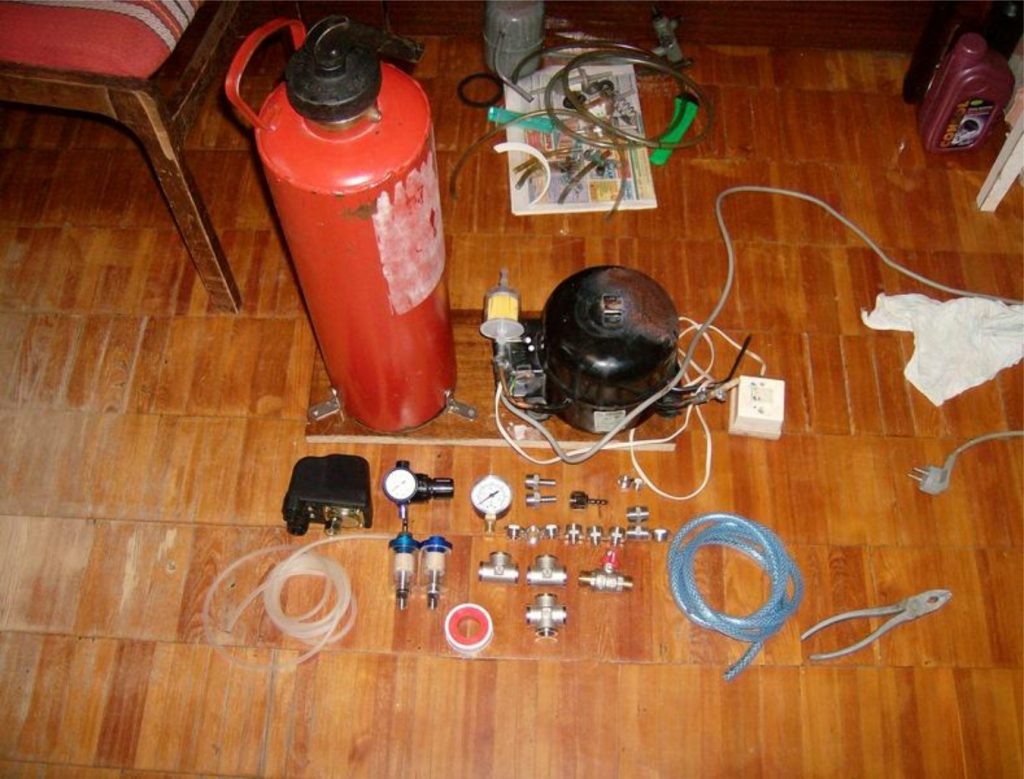
Preparation of equipment for a makeshift compressor station
When developing the compressor station scheme and compiling a list of additional equipment to it, the planned field of application should be taken into account. The larger the receiver and the pressure in it, the wider the possibilities of homemade work will be. The standard scheme includes the following details and mechanisms:
- Electronic pressure sensor. It turns off the engine when the set pressure parameters in the receiver are reached.
- Pressure gauge for measuring the degree of air compression.
- Safety valve.
- Air dryer when exiting the receiver.
- Air filter for installation on the inlet pipe of the compressor unit.
- Filter for cleaning the air stream under pressure from oil.
- Switch button.
- Wires, high pressure hoses and fittings with the required configuration.
- High pressure tank for the receiver.
- Ball valve that shuts off the air supply to the consumer at the system exit.
Ways to purchase equipment
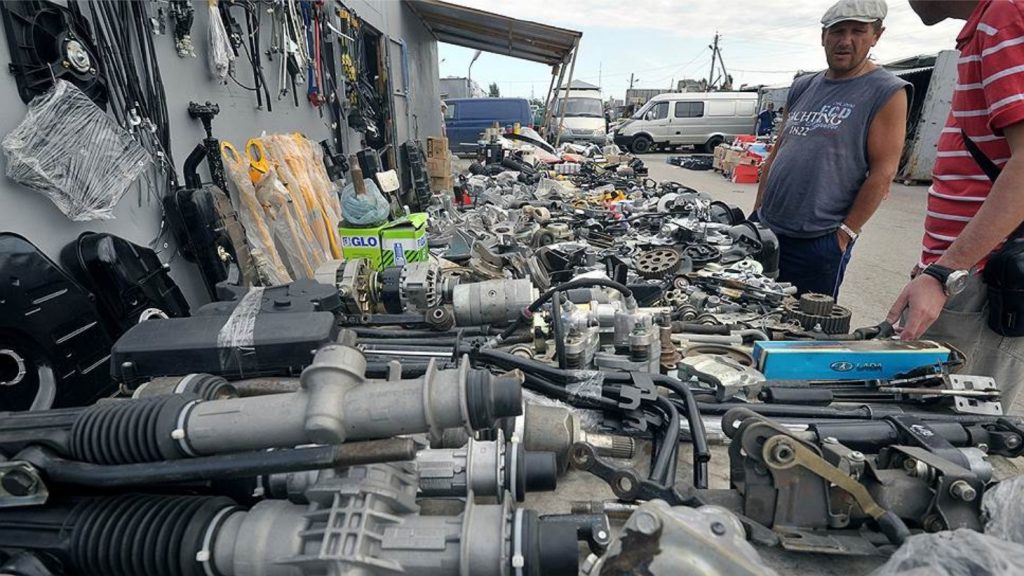
An old compressor from a refrigerator can be inexpensively bought on the used tool market
Most of the parts for a compressor station are easiest to buy at a plumbing store. There are specialized sites where all parts without exception can be ordered in a few clicks. The much cheaper equipment you need is available on the used tools market. It is acceptable to use cheap fuel filters, but using a conventional fitting and a metal sponge for washing dishes, you can quickly make a more reliable filter for rough cleaning of air from oil, which is installed on the output tube of the motor block.
Receiver problem
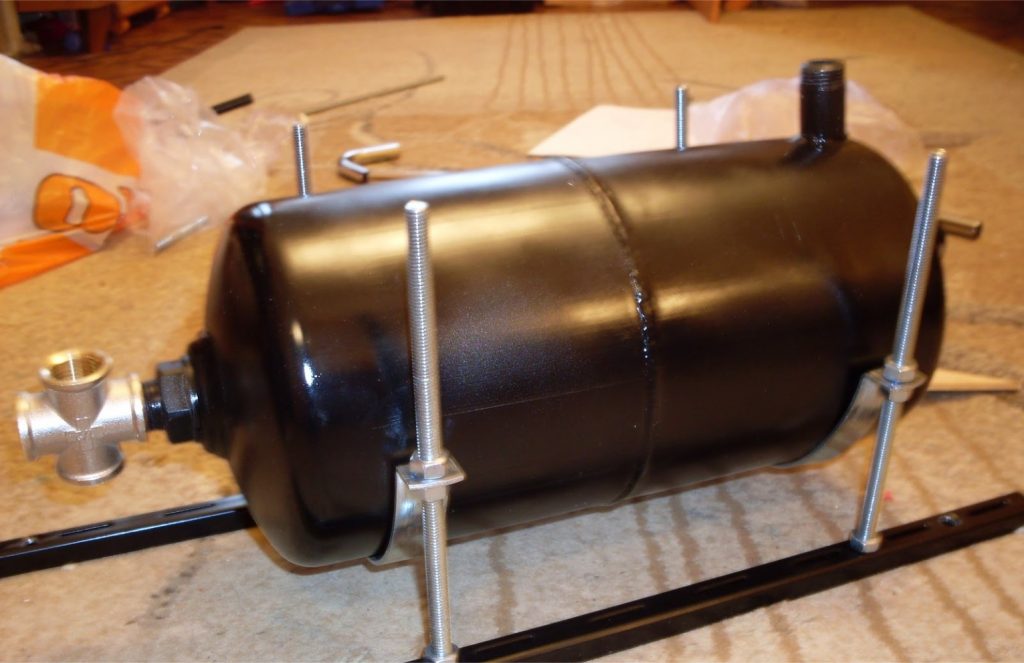
Homemade Welded Receiver
Cylinders for home-made compressor equipment are not available for sale. For this purpose, cylinders of various purposes and capacities are redone under the receiver:
- Propane and methane cylinders.
- Fire extinguishers.
- Cylinders for storing compressed air, carbon dioxide, oxygen and others.
- Home-made welded structures.
Attention: When using home-made housings for the receiver, it is necessary to take into account the degree of risk and explosion hazard of such a device.
The simplest option is a steel pipe of medium diameter with sealed plugs. The receiver must have at least 3 throughput nodes:
- Compressed air inlet from compressor.
- Outlet
- The condensate drain assembly from the cylinder, which should be located at the bottom point.
When using steel cylinders, the inlet and outlet tubes are welded by welding. The housing must withstand more than 10 atmospheres.
Preparation and connection of the compressor from the refrigerator for use in the compressor installation
When connecting the compressor unit, you can leave the same circuit that was originally provided - through the start relay.To this relay, you can connect the wires of the pressure sensor, which will interrupt the circuit after reaching the calculated pressure parameters in the receiver. Additional amenities include equipping the entire system with a push button switch and LED operation indicator. Before connecting to the unit, you can change the oil. Old oil is designed to work with freon. Special compressor oil for operation in the air will protect the motor from overheating and premature failure.
Installing the air filter on the air intake
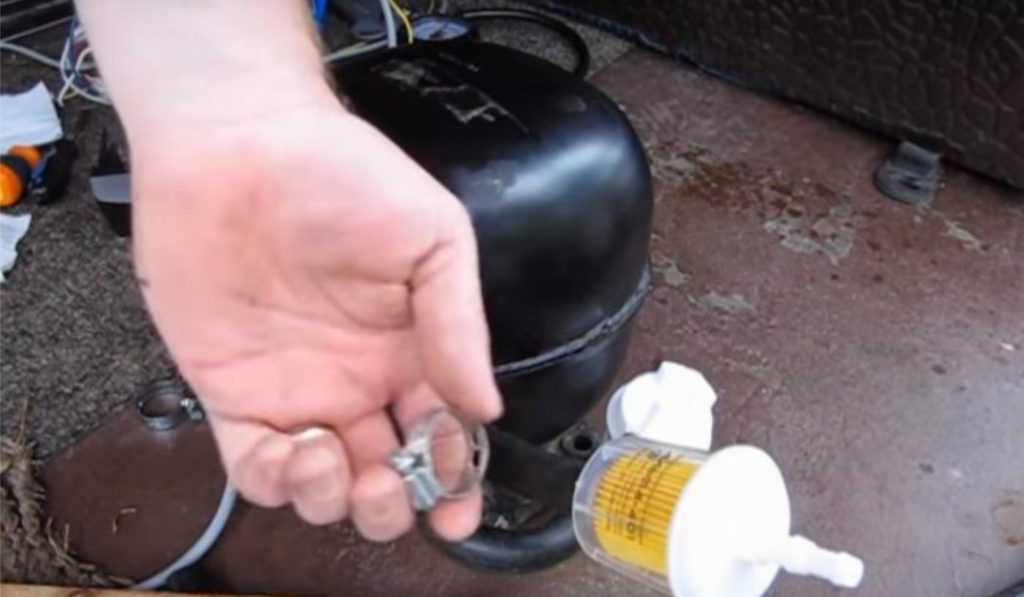
Installing a fuel filter on the compressor inlet pipe from the refrigerator to clean the air flow
To fit the air filter on the inlet tube, the simplest version of which is a plastic fuel filter, you can use either a soft rubber hose or a metal corner fitting with a threaded connection. It is easiest to squeeze a connecting soft tube, stretched over the plastic tip of the filter and the copper inlet, with a metal clamp.
Mounting the oil cleaner
The air stream coming from the unit contains a significant amount of oil, which can be filtered using a makeshift shutoff. A drainage hole with a tap should be provided in its housing through which it can be cleaned. It is allowed to install a cooling coil made of a metal tube between the oil shutoff device and the compressor unit.
Highway with measuring and control equipment
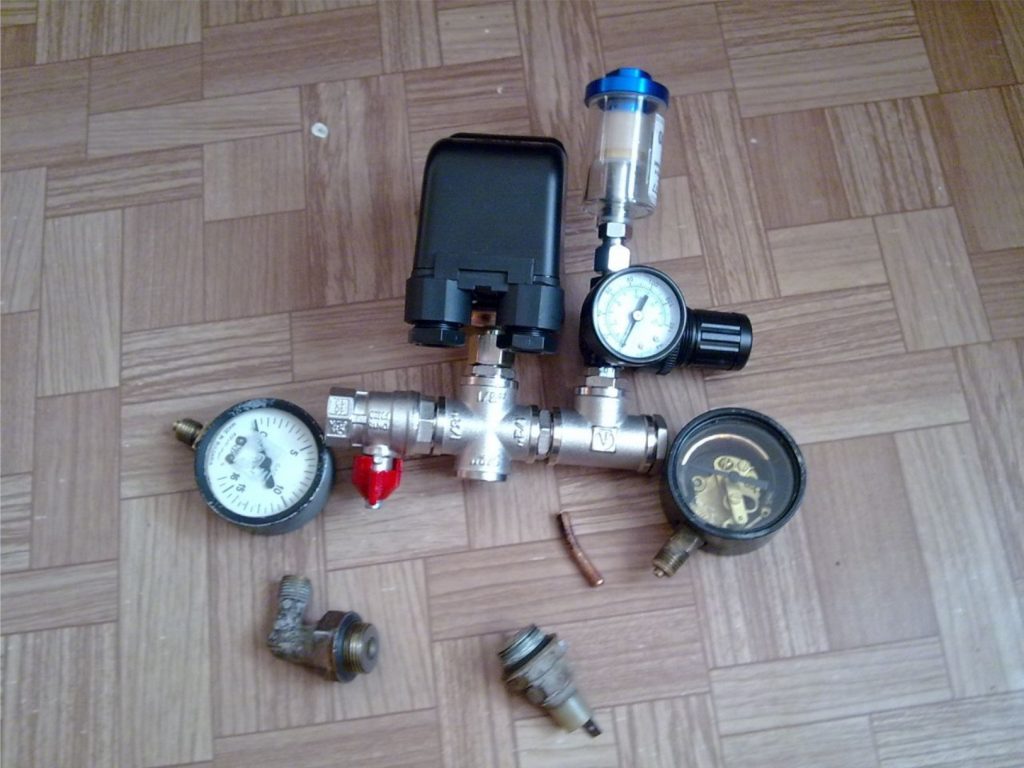
Preparation for assembly of the main line with instrumentation for the compressor station
All control and measuring devices are easiest to place on one highway. This will require ordinary metal tees from a plumbing store. On a single platform there is a system shutdown sensor when operating pressure is reached, a manometer, a device for cleaning the air from condensate accumulating in the receiver and a safety valve with which you can quickly dump excess air from the cylinder. At the exit of the highway, a control ball valve can be located. The main unit is connected to the storage cylinder either through its regular inlet or through a home-made input on its body.
The problem of connecting instrumentation
If the diameters of the instrumentation do not correspond to the dimensions of the available fitting, then in this case all the instruments can be mounted using plugs in which holes of the required size are drilled and a thread is cut with the appropriate pitch. Threaded connections are sealed with fum tape.
The problem of high pressure rubber tubes
Thick-walled oxygen hoses are one of the most affordable materials for connecting all parts of the compressor apparatus. But it should be borne in mind that the air stream when leaving the engine compartment will contain a large amount of oil that destroys rubber. For this reason, it is preferable to use metal (copper, or steel) tubes.
Do-it-yourself compressor maintenance
Maintenance of a homemade compressor station should be carried out taking into account the features of its configuration. The performance and tightness of all components should be checked periodically. A leak in the locking devices can be easily detected if a pressure measuring device is installed, which immediately shows its rapid loss. The performance of the pressure sensor can be easily monitored using a manometer, the readings of which can be recorded at the time of regular shutdown of the system after filling the air tank. You should also regularly drain condensate and oil from filters and cylinders.